42 cause and effect diagram six sigma
ss.ceDiag: Cause and Effect Diagram in SixSigma: Six Sigma ... The cause and effect diagram is also known as "Ishikawa diagram", and has been widely used in Quality Management. It is one of the Seven Basic Tools of Quality. Author(s) EL Cano References. Cano, Emilio L., Moguerza, Javier M. and Redchuk, Andres. 2012. Six Sigma with R. Statistical Engineering for Process Improvement, Use R!, vol. 36 Fishbone Diagram Six Sigma Template - Studying Diagrams The core purpose of Six Sigma. A fishbone diagram also known as a cause and effect diagram or Ishikawa diagram helps teams brainstorm the causes of a certain event. Identify the problem that negatively impacts your business performance or customer satisfaction.
Tree Diagrams for Six Sigma: Plain and Simple? The focus here is on four kinds of "trees" or hierarchical diagrams that become part of many Six Sigma projects: Cause-and-effect diagrams; Y-to-x flowdown diagrams; Functional analysis diagrams; Abstraction diagrams (KJ or affinity)
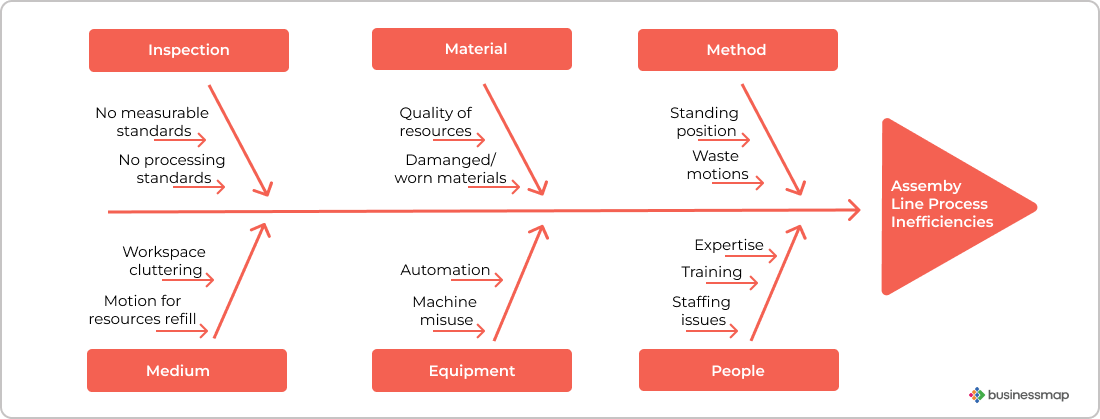
Cause and effect diagram six sigma
How to Complete the Six Sigma Cause and Effect Matrix The Cause and effect matrix is a Lean Six Sigma tool used to prioritize the key process input variables (KPIVs) based on priorities of customer outputs (KPOVs). In other words, it establish the correlation between process input variables to the customer's outputs during root cause analysis. How could the C&E Matrix help you in your project? Understanding Cause and Effect With a ... - Lean 6 Sigma There are several quality control tools in Six Sigma, one of them being the fishbone diagram. It is mainly used in root cause analysis, particularly in the Analyze phase of the DMAIC methodology. Sometimes you will hear it being called the cause and effect diagram when project managers are using it for quality management. Cause and Effect Diagrams - Management and Planning Tools ... Six Sigma skills are widely sought by employers both nationally and internationally. These skills have been proven to help improve business processes and performance. This course will introduce you to the purpose of Six Sigma and its value to an organization. You will learn about the basic principles of Six Sigma and Lean. Your instructors will introduce you to, and have you apply, some of the tools and metrics that are critical components of Six Sigma.
Cause and effect diagram six sigma. What is a Cause and Effect Diagram - Six Sigma Daily A Cause and Effect Diagram is a graphical tool for displaying a list of causes associated with a specific effect. It is also known as a fishbone diagram or an Ishikawa diagram (created by Dr. Kaoru Ishikawa, an influential quality management innovator). The graph organizes a list of potential causes into categories. admin — January 11, 2013. Creating a Fishbone Diagram for Six Sigma Analysis ... An Ishikawa or "fishbone" diagram is used in Six Sigma analysis of potential root causes of a problem. The project team brainstorms possible causes, organizes them in a way that looks like the layout of bones in a fish, and drills down to the root causes. This requires continually asking "why" and not just accepting the first reason given for a problem as a root cause. Cause and Effect Diagram (aka ... - Six Sigma Study Guide Cause and Effect Diagram Example. Fishbone diagrams are used to identify the root causes of a problem in the "Analyze" phase of Six Sigma's DMAIC (Define, Measure, Analyze, Improve, and Control). Example: XYZ is a valve manufacturing unit receiving persistent customer complaints about the valve diameter. Glossary: Cause and Effect Diagram | Lean Six Sigma Also known as a "Fishbone" or "Ishikawa Diagram"; categorical brainstorming tool used for determining root-cause hypothesis & potential causes for a specific effect. Skip to content Connect With Us Email: info@6sigma.com Phone: (866) 409-1363
Cause and Effect Diagram Definition - iSixSigma A cause and effect diagram is a visual tool used to logically organize possible causes for a specific problem or effect by graphically displaying them in increasing detail. It helps to identify root causes and ensures common understanding of the causes. It is also called an Ishikawa diagram. Fishbone Diagram, Ishakawa Diagram, Cause and Effect Diagram In a DMAIC Six Sigma project this tool is used in the MEASURE phase. It initiates the collection of the all root causes, x's, or inputs that contribute to the problem, also referred to as the effect or "Y". Often this beginning phase of subjective root cause analysis runs concurrently with the Measurement Systems Analysis (MSA). Objective: Cause and Effect Matrix aka X-Y ... - Six Sigma Study Guide Cause and effect matrix is a six sigma tool uses to prioritize the key process input variables (KPIVs) based on priorities of customer outputs (KPOVs). In other words it establish the correlation between process input variables to the customer's outputs during root cause analysis. Cause and effect matrix also called X-Y diagram, Prioritization matrix and correlation matrix. Six Sigma DMAIC Process - Analyze Phase - Data Door ... Six Sigma Pie Chart Cause and Effect Diagram / Fish Bone Diagram / Ishikawa Diagram: This is a visual tool used to brainstorm the probable causes for a particular effect to occur. Effect or the problem is analogously captured as the head of the fish and thus the name.
6Ms of Production (man, machine, material, method, mother ... The 6Ms of production - Manpower, Method, Machine, Material, Milieu and Measurement - is a mnemonic representing the characteristic dimensions [1] to consider when brainstorming during "cause and effect" problem-solving sessions. Capture and bin the issues (causes) under the 6M categories. R: Cause and Effect Diagram The cause and effect diagram is also known as "Ishikawa diagram", and has been widely used in Quality Management. It is one of the Seven Basic Tools of Quality. Author(s) EL Cano References. Cano, Emilio L., Moguerza, Javier M. and Redchuk, Andres. 2012. Six Sigma with R. Statistical Engineering for Process Improvement, Use R!, vol. 36 Fishbone Diagram (aka Cause & Effect Diagram) | Template ... It is also known as a Cause and Effect Diagram or an Ishikawa Diagram after its creator. Causes are often grouped into major categories, which are classically defined as the 6 Ms (or the 6 Ps): Man/Mind Power (People) Method (Process) Machines (Program) Materials (Product) Cause and Effect diagram - Six Sigma SPC Cause and Effect diagram. Also called a "Fishbone Diagram", (shape looks like a fish with the head being on the right and the tail on the left), or "Ishikawa Diagram", (created by Kaoru Ishikawa).Tool used to make assumptions of the root-cause and/or potential or common causes, for a specific effect.Embraced for use in six sigma, among other types of project management.
Cause and Effect Diagrams - Quality Tools and Six Sigma ... The Cause and Effect Diagram was created by Kaoru Ishikawa in the 1960s. It's a formal brainstorming tool for identifying possible root causes. The purpose of a Cause and Effect Diagram is to gather information and ideas from as many people as possible and to explore all possible causes of a problem.
Cause and Effect Diagrams - NINTHSIGMA Cause and Effect Diagram also known as the Fishbone Diagram, or the Ishikawa Diagram is a root cause analysis tool used in lean six sigma projects and is considered one of the seven basic tools of quality control. It was c reated by Kaoru Ishikawa to show the potential causes of a specific event at Kawasaki shipyards.
Getting the Most from a Cause and Effect Diagram - Six ... Cause-and-effect diagrams are one of the tools that Six Sigma professionals use to obtain the perspectives of individual members of a project team. The cause-and-effect diagram is a graphical brainstorming tool used to help capture the possible causes of a problem.
Cause & Effect Diagrams - Lean Six Sigma Training Guide Copy Cause & Effect Diagrams. Cause & Effect Diagrams or Ishikawa Diagrams, as they're also known, are one of the graphical tools that are used to check and categorize all the possible causes of a specific problem. Since it looks like a fish skeleton, some people tend to refer to this diagram as a "fishbone diagram" as well.
Using Regression Analysis to Enhance Cause and Effect ... Traditional Cause and Effect diagrams provide a good qualitative picture. Applying a simple regression analysis model using basic features of Excel can provide the quantitative data. Additionally, the results can be used in a cost benefit analysis to get a more definitive and convincing value proposition for those Six Sigma problems and projects.
How a Cause & Effect Diagram Helped Reduce Defects by 19% ... A great Lean Six Sigma process tool to use for situations like this, to ensure you are really uncovering all the possible causes of issues, is the Cause & Effect Diagram. This tool is also referred to as a Fishbone Diagram, or Ishakawa Siagram. Using a Cause & Effect Diagram at a Financial Services Company
Cause and Effect Tool in Six Sigma - Edraw - Edrawsoft Cause and Effect (Fishbone) Diagram. A cause and effect diagram, also known as a "fishbone" diagram, can help in brainstorming to identify possible causes of a problem and in sorting ideas into useful categories, which is a common tool using in six sigma programs for root cause analysis. The fishbone will help to visually display the many potential ...
Six Sigma Tutorial: Cause and Effect Diagram - YouTube Creating a cause and effect (Ishikawa or fishbone) diagram using Visio 2010 Beta. These diagrams are used in Six Sigma.Try our free sales and customer repor...
Cause & Effect Diagrams - SlideShare Cause & Effect Diagrams provides and overview of the Lean Six Sigma Tool. Lean Six Sigma Article by Master Black Belt, Steven Bonacorsi, Vice President at the … SlideShare uses cookies to improve functionality and performance, and to provide you with relevant advertising.
Fishbone Diagram - Lean Manufacturing and Six Sigma ... Also known as a Cause and Effect diagram, or Ishikawa diagram. The method was created by Kaoru Ishikawa in the 1960's. He created it to help employees avoid solutions that merely address the symptoms of a much larger problem. The defect or problem is shown as the fish's head on the right side (typically).
Cause and Effect Diagrams - Management and Planning Tools ... Six Sigma skills are widely sought by employers both nationally and internationally. These skills have been proven to help improve business processes and performance. This course will introduce you to the purpose of Six Sigma and its value to an organization. You will learn about the basic principles of Six Sigma and Lean. Your instructors will introduce you to, and have you apply, some of the tools and metrics that are critical components of Six Sigma.
Understanding Cause and Effect With a ... - Lean 6 Sigma There are several quality control tools in Six Sigma, one of them being the fishbone diagram. It is mainly used in root cause analysis, particularly in the Analyze phase of the DMAIC methodology. Sometimes you will hear it being called the cause and effect diagram when project managers are using it for quality management.
How to Complete the Six Sigma Cause and Effect Matrix The Cause and effect matrix is a Lean Six Sigma tool used to prioritize the key process input variables (KPIVs) based on priorities of customer outputs (KPOVs). In other words, it establish the correlation between process input variables to the customer's outputs during root cause analysis. How could the C&E Matrix help you in your project?
0 Response to "42 cause and effect diagram six sigma"
Post a Comment